Pulverized coal fired boiler pdf
The boiler system in consideration is a 500MW pulverized coal fired utility boiler. Schematic diagram of the boiler is shown in Figure 1. The boiler is of drum type with steam reheating. It has subcritical pressure of 170 kg/cm2 and forced circulation. It is fired with bituminous coal with tangentially corner fired combustion. There are total 8 numbers of Horizontal double ended ball mills
Coal dust is a fine powdered form of coal, which is created by the crushing, grinding, or pulverizing of coal. Because of the brittle nature of coal, coal dust can be created during mining , transportation, or by mechanically handling coal.
pulverized fuel boilers fire coal in differing configurations including wall firing, corner firing and in some cases for low volatile fuels arch firing. The coal being fired in these boilers is . 92 generally a high to medium quality bituminous coal which in many cases beneficiated through some type of washing. Foster Wheeler has designed and supplied over 130,000 MW’s of the type of solid
pulverized coal fired boiler with four burners and an originally specified turndown of 4 to l. The boiler’s The boiler’s generating capacity exceeds current load demands and significant fuel savings are available if oil firing can
Abstract. The Clean Coal Technology Demonstration Program (CCT) is a government and industry cofunded technology development effort to demonstrate a new generation of innovative coal utilization processes in a series of full-scale facilities.
In boilers with pulverized firing systems, about 80% of the ash in coal being fired is carried as fly ash. The other The other about 20% get collected as bottom ash.
This review includes the history of the boiler development beginning with the world’s first ultra-supercritical steam system, which began operation at the American Electric Power (AEP) Philo Station in 1957, through the development of the world’s largest boilers, the pulverized coal fired 1300 MW class. The most recent of the 1300 MW units began operation in 1990 at the Zimmer Power
Steady State Energy and Exergy Analysis of Pulverized Coal
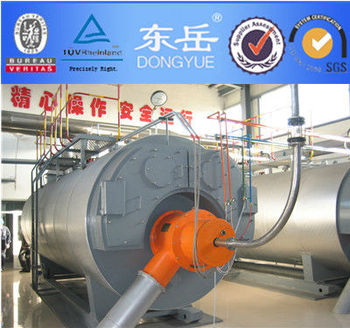
PULVERIZED COAL FIRED FURNACE Dalhousie University
Pulverized Coal Fired Boiler Application: Pulverized coal fired boiler is mainly used for industrial, commercial heating, it is a good quality boiler to replace traditional low efficient boiler.
Pulverized Fuel Boiler Most coal-fired power station boilers use pulverized coal, and many of the larger industrial water-tube boilers also use this pulverized fuel. This technology is well developed, and there are thousands of units around the world, accounting for well over 90% of coal-fired capacity. The coal is ground (pulverised) to a fine powder, so that less than 2% is +300 micro metre
Most coal fired power station boilers use pulverized coal. This technology is well developed, and there are thousands of units around the world, accounting for well over 90% of
A pulverised coal-fired boiler is an industrial boiler used in most of the thermal power plants in operation nowadays. It generates thermal energy by burning pulverised coal that is blown into
with coal in existing coal-fired boilers. In biomass cofiring, biomass can substitute for up In biomass cofiring, biomass can substitute for up to 20% of the coal used in the boiler.
Pulverized coal boilers fire finely powdered coal, typically with an average particle size of about 25 µm (0.001 in). Coal burns in suspension, like the combustion in an oil- or gas-fired boiler. Coal is pulverized in some type of large mill Pulverized coal is fired out into the furnace volume using burners that look somewhat like oil or gas burners. ME 416/516 B&W Pyrites trap Windbox
Coal-fired boiler systems generate approximately 38% of the electric power generation worldwide and will continue to be major contributors in the future. New pulverized coal-fired systems
Pulverized Coal Technology – Free download as PDF File (.pdf), Text File (.txt) or read online for free.
61 SIMULATION OF PULVERIZED COAL FIRED BOILER: REACTION CHAMBER C. P. Rodrigues, M. A. Lansarin, A. R. Secchi, and T. F. Mendes Grupo de Modelagem, Simulação
verized coal fired boiler. Clearly there is a need for improved mineral matter behavior predictive techniques. This paper will provide a statement of the ash deposition problem in pulverized

The biomass-mixed-firing pulverized coal fired boiler according to claim 1, further comprising a coal mill configured to mill a coal so as to produce the pulverized coal to be supplied to the pulverized coal …
performance of pulverized coal plants. For example; a large utility boiler can be tested and found to be For example; a large utility boiler can be tested and found to be meeting the original design boiler efficiency by completing an ASME boiler heat loss method performance
Pulverized coal-fired boiler – Wikipedia 2018-11-12 · A pulverized coal-fired boiler is an industrial or utility boiler that generates thermal energy by burning pulverized coal (also known as powdered coal or coal dust since it is as fine as face powder in cosmetic makeup) that is blown into the firebox..
PULVERIZED COAL FIRED BOILERS FOR LODŽ, POLAND UNIS Power took part in a challenging coal fired power project for Veolia Energia Łódź S.A. in Poland where German based EPC contractor was responsible for the turnkey delivery of

estimates of performance and order-of-magnitude costs of conventional pulverized coal (PC) and integrated gasification combined cycle (IGCC) power plants. The estimates cover a …
MEMBRANE WALLS DEPOSITS IN PULVERIZED COAL FIRED BOILERS Fly ash Wall deposits. COMBUSTION AND FUELS PHYSICAL AND CHEMICAL PROCESSES OF MINERAL MATTER CONVERSION DURING COAL COMBUSTION During coal combustion mineral matter undergoes conversion: – physical: melting, evaporation, sublimation and condensation, – chemical: …
4. High efficient low NOx combustion technologies for coal fired unit Coal fired power plants are major energy sources world’ wide in view of their stable and economical energy supply.
Development of Computer Program for Combustion Analysis in Pulverized Coal-fired Boilers 78 concentration, it is necessary to estimate the
cost oil-fired power plants to utilize pulverized petroleum coke (“pet coke”) , a by-product of the oil refining process, as a replacement fuel with no other support fuels required.
A pulverized coal-fired boiler is an industrial or utility boiler that generates thermal energy by burning pulverized coal (also known as powdered coal or coal dust since it is as fine as face powder in cosmetic makeup) that is blown into the firebox.
CALCIUM COMPOUNDS DURING THE COMBUSTION OF PULVERIZED COAL P. L. Case, M. P. Heap, C. N allow simulataneous control of sulfur and nitrogen oxide emissions from pulverized coal fired boilers. 2. EXPERIMENTAL Thus retention of the sulfur It A bench scale facility has been constructed which is capable of duplicating the history of the solid particles (coal and sorbent) and …
Pulverized Coal Fired Power Plant Performance The performance of an electric power plant is ultimately measured in terms of the amount of electricity it produces (useful output) per unit of fuel burned (required input).
The particle size distribution (PSD) is critical for pulverized-coal combustion in coal-fired power-plant boilers. However, the PSD might not necessarily be an independent variable in combustion analysis.
Pulverized coal-fired boilers are available in capacities over 1000 MW and typically require better quality fuels. Advanced Pulverized Coal Combustion (PC) Technology Pulverized Coal …
Once through boiler PDF Free Download – edoc.site
The Development of a Slagging and Fouling Predictive Methodology for Large Scale Pulverised Boilers Fired with Coal/Biomass Blends By Piotr Patryk PŁAZA M.Sc., Power and Mechanical Engineering M.Sc., Environmental Engineering A Thesis submitted to Cardiff University for the Degree of Doctor of Philosophy in Mechanical Engineering Institute of Energy Cardiff School of Engineering …
COMBUSTION AND FUELS Types of boiler furnaces Coal-fired boilers can be classified regarding the type of a furnace: grate boilers (stoker), pulverized fuel-fired boilers (PF),
Introduction In a pulverized coal-fired boiler of a large power plant, an oxygen . analyzer is essential for combustion control. Exhaust gases from
and economic feasibility of producing a generic refuse derived fuel supplement for pulverized coal fired boilers was developed at Detroit Edison in – teledyne laars mighty therm boiler manual 2 Your Need: Changes in fuel characteristics or boiler operations lead to fireside slagging, fouling, and increased wear of boiler parts and fuel handling equipment.
31/12/2006 · A preliminary economic assessment of the enhanced low NOx pulverized coal burner system was conducted based on three utility boilers studied under the DOE/NETL – ALSTOM program titled “Ultra Low NOx Integrated System for NOx Emission Control from Coal-Fired Boiler”
Coal, petroleum-based oils, and natural gas are fossil fuels commonly fired in ICI boilers. However, However, other forms of solid, liquid, or gaseous fuel derived from these fossil fuels are …
PF Supercritical Boi lers ii Australia Summary The use of super-critical (SC) steam conditions has been applied in recent Australian, European and Japanese coal fired power stations.
Harness State-of-the-Art Computational Modeling Tools Computational Modeling of Pulverized Coal Fired Boilers successfully establishes the use of computational modeling as an effective means to simulate and enhance boiler performance.
The model was coupled with a comprehensive combustion code to predict the flow field, the temperature field and the deposit growth behavior in a pulverized coal-fired boiler. Some useful conclusion can be deduced to guide the investigation of deposit growth. The deposits grow rapidly at those places where the particles’ impacting probability and the temperature of wall surface are high. The
27/03/2016 · wood powder coal powder burner for boiler, coating, drying, heat equipment, foundry and other industries, burning of biomass fuels to replace oil, …
Simulation and testing of PFS at existing pulverized coal-fired boilers of TPP confirmed the technical feasibility, environmental and energy efficiency of no-fuel oil boilers start-up and pulverized coal
Upper limits of Average Grate heat release rate, q F Boiler capacity Upper limit of q F in MW/m2 (ST= Softening Temperature) (tons/h)* ST 1300 C ST =1300 C ST 1300 C
Pulverized coal fired boilers use coal of several tens of micrometers in size and then fire such pulverized coal in a suspended state inside the boiler furnace.
The technology of biomass co-firing in large pulverized coal-fired boilers seems to be the most cost-effective way of biomass utilization due to the higher boiler efficiency in comparison with 100% firing biomass in smaller boilers [8]. Despite the advantages, co-firing biomass with pulver-ized coal imposes some serious problems (connected with specific characteristics of biomass fuels) that
Particle Size Distribution as a Nonindependent Variable
combustion process in a front wall pulverized coal fired utility boiler of 350 MW with 24 swirl burners installed at the furnace front wall. Five different cases with 100, 95, 85, 70 and 50% boiler full load were simulated. Comparisons were addressed, with good agreement between predicted and measured results in the boiler for all but one case thus validating the models and the algorithm
Coal-Fired Boilers 87 Steam Turbines 90 Combustion Turbines 92 Stationary Diesel Engine Turbines 92 Annex 4. OEMs in India 95 List of Technical Reports 97 Figures 2.1: Average Price of Crude Oil Worldwide 4 2.2: Effect of Size on Cost of Gas Turbine Combined Cycle Units 10 2.3: Effect of Size on Cost of Pulverized Coal-Fired Plants 11 3.1: Cost Indexes for 316 Stainless Steel, Nickel, and
Pulverized coal fired boilers the total losses account to about 12 to 14 %. Roughly 50% of the losses can be tuned to the optimum and the other 50 % is governed by fuel properties like hydrogen in fuel, moisture in fuel and ambient air conditions. The main two losses in boiler that can be tuned by operator are carbon loss and dry gas loss.
A pulverized coal-fired boiler is an industrial or utility boiler that generates thermal energy by burning pulverized coal also known as powdered coal or coal dust.
In coal-fired boilers the required air–coal ratio of the mixture leaving the pulverizers ranges from 1.2:1 to about 2.2:1 and is generally near 2:1 for vertical spindle mills. Thus the amount of primary air is relatively low compared with the amount of
Coal-fired water tube boiler systems generate approximately 38% of the electric power generation worldwide and will continue to be major contributors in the future. Pulverized coal fired boilers,
THE I OPERATIONAL PARAMETERS ON BOILER ERFORMANCE AN
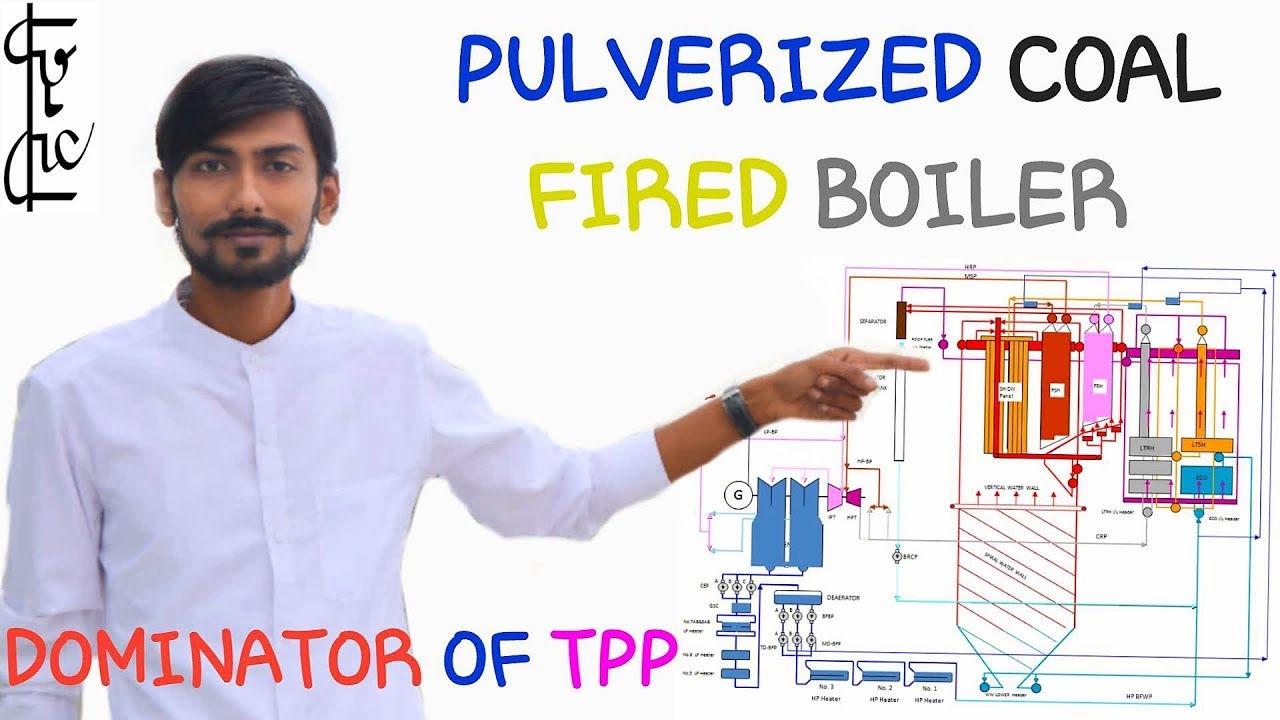
Measurement of O2 Concentration in Exhaust Gases from
Boiler fireside fouling and corrosion problems are mainly restricted to coal and oil fired installations. There are very few reported incidents of corrosion associated with gas fired units, the problem here being mainly confined to overheating due to incorrect operational firing arrangements. Modern high pressure coal firing boilers are all designed to fire pulverized fuel. Coal is delivered
ISSN(PRINT):2394-6202,(ONLINE):2394-6210,VOLUME-1,ISSUE-6,2015 23 Abstract— The demand of electricity is increasing nowadays and has raised the
PDF This work is part of a joint project to built a computational tool for power plant simulation, dealing specifically with the reaction chamber (place of the boiler where the fuel is burned).
Computational modeling of PC boilers Pulverized Coal Fired Boilers PDF by Vivek V. Ranade Devkumar F. Gupta. Pulverized coal fired boilers have been and will be the mainstay of coal based power generation worldwide. Such pulverized coal boilers are complex chemical reactors comprising many processes such as gas-solid flows, combustion, heat
lignite and the firing configuration of the boiler. Pulverized coal-fired units fire much or all of the lignite in suspension. Cyclone furnaces collect much of the ash as molten slag in the furnace itself. Stokers (other than spreader) retain a large fraction of the ash in the fuel bed and bottom ash. Spreader stokers fire about 15 percent of the coal in suspension and the remainder in a bed
1 of 15 Design Considerations for Pulverized Coal Fired Boilers Combusting Illinois Basin Coals Dianna Tickner Peabody Energy St. Louis, Missouri
The Development of a Slagging and Fouling Predictive

Clean coal reference plants Pulverized encoal PDF fired
(PDF) Developments in Pulverized Coal-Fired Boiler . 2017/09/14· PDF Coal-fired boiler systems generate approximately 38% of the electric power generation worldwide and will continue to be major contributors in the future.
Pulverized coal (pulverized fuel-pf) has been fired in rotary cement kilns (see Kilns) and boiler furnaces (see Boilers). The latter are basically boxes lined with tubes in which water is evaporated and contain a water/steam mixture.
Steady State Energy and Exergy Analysis of Pulverized Coal Fired Boiler Lalatendu Pattanayak Steag Energy Services India Pvt. Ltd., A-29, Sector-16,
The paper presents results of numerical modeling of pulverized coal combustion process in the front wall coal-fired boiler. The developed numerical model of the coal combustion process included particle heating, devolatilization, char combustion, as well as turbulent flow and radiative heat transfer.
Coal Fired Boiler Industrial BoilerOil & Gas fired
Numerical study of a large-scale pulverized coal-fired
https://en.m.wikipedia.org/wiki/Coal_burner
pulverized coal is crushed into kancelariaurbanowicz.eu
– Computational Modeling Of Pulverized Coal Fired Boilers
SIMULATION OF PULVERIZED COAL FIRED BOILER REACTION
PULVERIZED COAL FURNACES Thermopedia
Modeling Approaches to Predict Biomass Co-firing with
pulverized coal is crushed into kancelariaurbanowicz.eu
Extension of Cogeneration Capability by Increasing
Development of Computer Program for Combustion Analysis in Pulverized Coal-fired Boilers 78 concentration, it is necessary to estimate the
Pulverized Coal Fired Boiler Application: Pulverized coal fired boiler is mainly used for industrial, commercial heating, it is a good quality boiler to replace traditional low efficient boiler.
This review includes the history of the boiler development beginning with the world’s first ultra-supercritical steam system, which began operation at the American Electric Power (AEP) Philo Station in 1957, through the development of the world’s largest boilers, the pulverized coal fired 1300 MW class. The most recent of the 1300 MW units began operation in 1990 at the Zimmer Power
Pulverized coal (pulverized fuel-pf) has been fired in rotary cement kilns (see Kilns) and boiler furnaces (see Boilers). The latter are basically boxes lined with tubes in which water is evaporated and contain a water/steam mixture.
4. High efficient low NOx combustion technologies for coal fired unit Coal fired power plants are major energy sources world’ wide in view of their stable and economical energy supply.
Pulverized Coal Technology – Free download as PDF File (.pdf), Text File (.txt) or read online for free.
The boiler system in consideration is a 500MW pulverized coal fired utility boiler. Schematic diagram of the boiler is shown in Figure 1. The boiler is of drum type with steam reheating. It has subcritical pressure of 170 kg/cm2 and forced circulation. It is fired with bituminous coal with tangentially corner fired combustion. There are total 8 numbers of Horizontal double ended ball mills
pulverized coal fired boiler with four burners and an originally specified turndown of 4 to l. The boiler’s The boiler’s generating capacity exceeds current load demands and significant fuel savings are available if oil firing can
and economic feasibility of producing a generic refuse derived fuel supplement for pulverized coal fired boilers was developed at Detroit Edison in
Upper limits of Average Grate heat release rate, q F Boiler capacity Upper limit of q F in MW/m2 (ST= Softening Temperature) (tons/h)* ST 1300 C ST =1300 C ST 1300 C
PF Supercritical Boi lers ii Australia Summary The use of super-critical (SC) steam conditions has been applied in recent Australian, European and Japanese coal fired power stations.
Computational modeling of PC boilers Pulverized Coal Fired Boilers PDF by Vivek V. Ranade Devkumar F. Gupta. Pulverized coal fired boilers have been and will be the mainstay of coal based power generation worldwide. Such pulverized coal boilers are complex chemical reactors comprising many processes such as gas-solid flows, combustion, heat
The technology of biomass co-firing in large pulverized coal-fired boilers seems to be the most cost-effective way of biomass utilization due to the higher boiler efficiency in comparison with 100% firing biomass in smaller boilers [8]. Despite the advantages, co-firing biomass with pulver-ized coal imposes some serious problems (connected with specific characteristics of biomass fuels) that
29 replies on “Pulverized coal fired boiler pdf”
Leave a CommentPulverized Coal Fired Boiler Application: Pulverized coal fired boiler is mainly used for industrial, commercial heating, it is a good quality boiler to replace traditional low efficient boiler.
Coal Fired Boiler Industrial BoilerOil & Gas fired
Numerical study of a large-scale pulverized coal-fired
PF-Fired Supercritical Boilers Steam Forum
The particle size distribution (PSD) is critical for pulverized-coal combustion in coal-fired power-plant boilers. However, the PSD might not necessarily be an independent variable in combustion analysis.
PULVERIZED COAL FIRED FURNACE Dalhousie University
The particle size distribution (PSD) is critical for pulverized-coal combustion in coal-fired power-plant boilers. However, the PSD might not necessarily be an independent variable in combustion analysis.
US9068746B2 Biomass-mixed-firing pulverized coal fired
(PDF) Developments in Pulverized Coal-Fired Boiler Technology
Pulverized coal fired boilers use coal of several tens of micrometers in size and then fire such pulverized coal in a suspended state inside the boiler furnace.
Computational Modeling of PC Boilers Boilersinfo
combustion process in a front wall pulverized coal fired utility boiler of 350 MW with 24 swirl burners installed at the furnace front wall. Five different cases with 100, 95, 85, 70 and 50% boiler full load were simulated. Comparisons were addressed, with good agreement between predicted and measured results in the boiler for all but one case thus validating the models and the algorithm
PULVERIZED COAL FURNACES Thermopedia
1.7 Lignite Combustion epa.gov
Harness State-of-the-Art Computational Modeling Tools Computational Modeling of Pulverized Coal Fired Boilers successfully establishes the use of computational modeling as an effective means to simulate and enhance boiler performance.
OVERVIEW OF COAL ASH DEPOSITION IN BOILERS
Technology comparison of CFB versus pulverized-fuel firing
PULVERIZED COAL FURNACES Thermopedia
performance of pulverized coal plants. For example; a large utility boiler can be tested and found to be For example; a large utility boiler can be tested and found to be meeting the original design boiler efficiency by completing an ASME boiler heat loss method performance
Steady State Energy and Exergy Analysis of Pulverized Coal
CALCIUM COMPOUNDS DURING THE COMBUSTION OF PULVERIZED COAL P. L. Case, M. P. Heap, C. N allow simulataneous control of sulfur and nitrogen oxide emissions from pulverized coal fired boilers. 2. EXPERIMENTAL Thus retention of the sulfur It A bench scale facility has been constructed which is capable of duplicating the history of the solid particles (coal and sorbent) and …
Review on Combustion Optimization Methods in Pulverised
The model was coupled with a comprehensive combustion code to predict the flow field, the temperature field and the deposit growth behavior in a pulverized coal-fired boiler. Some useful conclusion can be deduced to guide the investigation of deposit growth. The deposits grow rapidly at those places where the particles’ impacting probability and the temperature of wall surface are high. The
Coal America’s Energy Future Vol. 2
In boilers with pulverized firing systems, about 80% of the ash in coal being fired is carried as fly ash. The other The other about 20% get collected as bottom ash.
Plasma-assisted ignition and combustion of pulverized coal
THE CAPTURE AND RETENTION OF SULFUR SPECIES BY CALCIUM
PULVERIZED COAL FIRED BOILERS FOR unispower.cz
27/03/2016 · wood powder coal powder burner for boiler, coating, drying, heat equipment, foundry and other industries, burning of biomass fuels to replace oil, …
Pulverized Coal Fired Boiler valanhighschool.com
How to Run a Coal Fired Boiler at the Best Efficiency
Extension of Cogeneration Capability by Increasing
COMBUSTION AND FUELS Types of boiler furnaces Coal-fired boilers can be classified regarding the type of a furnace: grate boilers (stoker), pulverized fuel-fired boilers (PF),
Coal dust Wikipedia
Coal America’s Energy Future Vol. 2
BURNING IN BOILER FURNACES Politechnika Wrocławska
The Development of a Slagging and Fouling Predictive Methodology for Large Scale Pulverised Boilers Fired with Coal/Biomass Blends By Piotr Patryk PŁAZA M.Sc., Power and Mechanical Engineering M.Sc., Environmental Engineering A Thesis submitted to Cardiff University for the Degree of Doctor of Philosophy in Mechanical Engineering Institute of Energy Cardiff School of Engineering …
1.7 Lignite Combustion epa.gov
and economic feasibility of producing a generic refuse derived fuel supplement for pulverized coal fired boilers was developed at Detroit Edison in
(PDF) SIMULATION OF PULVERIZED COAL FIRED BOILER REACTION
Pulverized Coal Technology Coal Boiler
performance of pulverized coal plants. For example; a large utility boiler can be tested and found to be For example; a large utility boiler can be tested and found to be meeting the original design boiler efficiency by completing an ASME boiler heat loss method performance
Fossil Fuel Fired Boiler Air and Gas Path
27/03/2016 · wood powder coal powder burner for boiler, coating, drying, heat equipment, foundry and other industries, burning of biomass fuels to replace oil, …
Plasma-assisted ignition and combustion of pulverized coal
Advanced Development of Pulverized Coal Firing Technologies
THE I OPERATIONAL PARAMETERS ON BOILER ERFORMANCE AN
MEMBRANE WALLS DEPOSITS IN PULVERIZED COAL FIRED BOILERS Fly ash Wall deposits. COMBUSTION AND FUELS PHYSICAL AND CHEMICAL PROCESSES OF MINERAL MATTER CONVERSION DURING COAL COMBUSTION During coal combustion mineral matter undergoes conversion: – physical: melting, evaporation, sublimation and condensation, – chemical: …
1.7 Lignite Combustion US EPA
1 of 15 Design Considerations for Pulverized Coal Fired Boilers Combusting Illinois Basin Coals Dianna Tickner Peabody Energy St. Louis, Missouri
Coal Fired Boiler Industrial BoilerOil & Gas fired
Computational Modeling Of Pulverized Coal Fired Boilers
Applying the Fundamentals for Best Heat Rate Performance
and economic feasibility of producing a generic refuse derived fuel supplement for pulverized coal fired boilers was developed at Detroit Edison in
Design Considerations for Pulverized Coal Fired Boilers
Simulation and testing of PFS at existing pulverized coal-fired boilers of TPP confirmed the technical feasibility, environmental and energy efficiency of no-fuel oil boilers start-up and pulverized coal
1.7 Lignite Combustion US EPA
Technology comparison of CFB versus pulverized-fuel firing
Most coal fired power station boilers use pulverized coal. This technology is well developed, and there are thousands of units around the world, accounting for well over 90% of
Enhanced Combustion Low NOx Pulverized Coal Burner
PULVERIZED COAL FIRED FURNACE Dalhousie University
Development of Computer Program for Combustion Analysis in Pulverized Coal-fired Boilers 78 concentration, it is necessary to estimate the
Enhanced Combustion Low NOx Pulverized Coal Burner
Pulverized and Cyclone-Fired Boilers
Upper limits of Average Grate heat release rate, q F Boiler capacity Upper limit of q F in MW/m2 (ST= Softening Temperature) (tons/h)* ST 1300 C ST =1300 C ST 1300 C
Once through boiler PDF Free Download – edoc.site
(PDF) Developments in Pulverized Coal-Fired Boiler Technology
How to Run a Coal Fired Boiler at the Best Efficiency
Pulverized Fuel Boiler Most coal-fired power station boilers use pulverized coal, and many of the larger industrial water-tube boilers also use this pulverized fuel. This technology is well developed, and there are thousands of units around the world, accounting for well over 90% of coal-fired capacity. The coal is ground (pulverised) to a fine powder, so that less than 2% is +300 micro metre
Pulverized Coal Fired Boiler valanhighschool.com
THE CAPTURE AND RETENTION OF SULFUR SPECIES BY CALCIUM
Pulverized Fuel Boiler Most coal-fired power station boilers use pulverized coal, and many of the larger industrial water-tube boilers also use this pulverized fuel. This technology is well developed, and there are thousands of units around the world, accounting for well over 90% of coal-fired capacity. The coal is ground (pulverised) to a fine powder, so that less than 2% is +300 micro metre
THE I OPERATIONAL PARAMETERS ON BOILER ERFORMANCE AN
MEMBRANE WALLS DEPOSITS IN PULVERIZED COAL FIRED BOILERS Fly ash Wall deposits. COMBUSTION AND FUELS PHYSICAL AND CHEMICAL PROCESSES OF MINERAL MATTER CONVERSION DURING COAL COMBUSTION During coal combustion mineral matter undergoes conversion: – physical: melting, evaporation, sublimation and condensation, – chemical: …
Numerical study of a large-scale pulverized coal-fired
Design Considerations for Pulverized Coal Fired Boilers
PDF This work is part of a joint project to built a computational tool for power plant simulation, dealing specifically with the reaction chamber (place of the boiler where the fuel is burned).
Review on Combustion Optimization Methods in Pulverised
Pulverized coal burner coal powder burner for boiler
Pulverized coal fired boilers use coal of several tens of micrometers in size and then fire such pulverized coal in a suspended state inside the boiler furnace.
Measurement of O2 Concentration in Exhaust Gases from
OPTIMIZATION OF COMBUSTION IN PULVERIZED COAL FIRED
Pulverized coal boilers fire finely powdered coal, typically with an average particle size of about 25 µm (0.001 in). Coal burns in suspension, like the combustion in an oil- or gas-fired boiler. Coal is pulverized in some type of large mill Pulverized coal is fired out into the furnace volume using burners that look somewhat like oil or gas burners. ME 416/516 B&W Pyrites trap Windbox
Coal America’s Energy Future Vol. 2
Comments are closed.